BOX CULVERTS
APPLICATION Specifications
There are a variety of ways to seal box culverts. The sealing solution – and the products and installation methods recommended to achieve each sealing solution – depends heavily on the structure’s end use, service conditions, and surrounding environment. Some factors to consider are whether the structure will convey or hold water, the depth of bury, the water table depth, whether the structure is required to be watertight, and whether chemicals or contaminants are expected to be in contact with the structure, among others. ConSeal can help provide an overview of terminology, applications, and considerations for the most common box culvert situations.
Consult with the Concrete Sealants engineering team for specific guidance.
SELECTING THE PROPER SEALANT
WHAT TYPE OF SEALING MATERIAL IS NEEDED?
Joint sealants are designed to create a gasket in a compression joint between two mating concrete surfaces. The sealant is intended to prevent soil, silt, and moisture intrusion as well as resist varying levels of hydrostatic pressure in certain conditions. The sealing materials required for a job depend on the project specifics including the end use of the structure, soil and site conditions, depth of bury, and structure dimensions, among others.
If no special circumstances exist, CS-102 or CS-202 may be an appropriate preformed flexible joint sealant for the job. In situations where oil or jet fuel may be present, a hydrocarbon-resistant sealant like CS-440 may be required. If chemicals will be present in the surrounding groundwater or in the water or wastewater traveling through the structure, a sealant with robust chemical resistance like CS-5000 may be needed. For potable water applications, sealant safe for use with drinking water, like CS-665, should be used.
Some scenarios may only require use of preformed flexible joint sealant with exterior joint wrap, while other scenarios may require a suite of products to achieve the desired performance in service including a combination of some or all of the following: preformed flexible joint sealant, waterstop sealant, gun-grade sealant, external joint wrap, primer, and adhesive.
WITH WHICH STANDARDS DO SEALING MATERIALS NEED TO COMPLY?
Generally, ASTM or AASHTO standards are specified for most joint sealing material. These standards define the composition and performance requirements of different products, including preformed flexible joint sealant, external joint wrap, and gun-grade material.
ASTM C990, “Standard Specification for Joints for Concrete Pipe, Manholes, and Precast Box Sections Using Preformed Flexible Joint Sealants.”
ASTM C877, “Standard Specification for External Sealant Bands for Concrete Pipe, Manholes, and Precast Box Sections.”
ASTM C920, “Standard Specification for Elastomeric Joint Sealants.”
In some cases, such as hydrocarbon or chemical resistance, a special sealant material that does not have an applicable ASTM standard must be used.
HOW MUCH SEALANT IS NEEDED?
The answer is as varied as the types and sizes of concrete box culvert sections produced. A misconception is that more joint sealant is better. However, too much sealant – or too little sealant – can result in leaky joints. The amount of sealant required is based on the structure’s dimensions and joint details, and the volume of sealant needed to sufficiently fill the joint gap.
Ideally, sealant coverage is preferred throughout as much of the wall thickness and joint width as possible. A minimum compressed sealant width in the joint of about 2”-3” is common, but a greater width of coverage is preferred. A maximum dry fit joint gap of ½” is recommended, and it is preferred that the joint be as tight as possible.
Preformed flexible joint sealants work best when they are compressed more. Generally, at least 50% sealant compression is required.
Preformed flexible joint sealants are manufactured in a variety of heights, widths, cross-sectional areas, and roll lengths, so there may be more than one way to achieve the required sealant volume. Additionally, the required volume of sealant may be achieved by using two or even three smaller strips of sealant rather than one larger strip of sealant. Consideration should also be given to the height of the sealant vs. the dry fit joint gap and the ability to compress the sealant adequately.
WHAT SHAPE OF SEALANT IS NECESSARY?
As sealant compresses, it retains its cross-sectional area. That is, as sealant compresses and gets thinner, the compressed sealant becomes wider proportionally. As a result, the cross-sectional area of the compressed sealant will be roughly equivalent to the non-compressed sealant.
As the sealant is compressed, the force required to achieve further sealant compression increases as a function of the percentage of compression achieved thus far. Time, temperature, force, and the sealant composition affect the compression rate. For instance, the pressure needed to compress the sealant the initial 10% to 50% may range from 2 psi to 4 psi. As the sealant is compressed, the sealant increases in width and the surface area to which the compression force is applied increases. Eventually, the area reaches a point of equilibrium with the designed resistance force of the sealant and compression will stop. An analogy to describe this is the use of snow shoes to distribute a person’s weight to allow them to walk across snow without sinking. The person’s weight remains the same (as does the force applied to the sealant), however the area across which the person’s weight is applied is increased by the use of snow shoes (and the sealant area to which the compression force is applied is increased as the sealant compresses), which reduces the pressure applied to the snow (and similarly reduces the pressure applied to the sealant, in psi).
WHAT IS SEALANT ADHESION AND WHY DOES IT MATTER?
How well the sealant adheres to the concrete affects the joint’s hydrostatic resistance. Water finds the path of least resistance, and if the concrete joint surface is not properly prepared or the concrete has a particularly porous surface, water can absorb into the concrete, bypass the sealing materials, and potentially compromise the system’s watertightness. This can result in wetness in or near the joint. Sealant will adhere best to a dry, clean, dense, and well-cured concrete surface that is free of dust, dirt, form release agent, and other substances that inhibit bonding. Use a ConSeal primer on the concrete surface before applying sealant to improve the sealant’s adhesion to concrete. A properly primed concrete surface will provide improved sealant and coating performance when compare to an unprimed concrete surface.
THE PROPER SEALING METHOD
HOW SHOULD PREFORMED FLEXIBLE JOINT SEALANT BE INSTALLED?
There two primary methods for installing preformed flexible joint sealant on box culvert joint faces, and the ideal methodology for each application depends heavily on the structure’s end use and the structure’s joint anatomy. Both methods are used to create a continuous seal and a continuous rope of joint sealant around the structure’s joint, however they employ different strategies to achieve the continuous perimeter of sealant.
WHERE SHOULD THE SEALANT BE PLACED?
Sealant placement is critical for any application. The best practice is to place sealant where the concrete touches tightest. It is also preferred to fill the annular space as much as possible.
For soil-tight or silt-tight box culvert applications, use either sealant installation Method A (continuous) or sealant installation Method B (non-continuous). For complete watertight applications, use sealant installation Method A. Method A involves fully encapsulating the interior of the bell with sealant. Use one of ConSeal’s adhesive sealants like CS-1550 to attach sealant to the vertical and inverted sections of the bell for a continuous sealant application. Method B involves placing sealant on the bell in the angled (sloped) joint surface along the bottom half of the structure, and 6” above the center line on each side. On the bell end, the sealant should be placed on the slope, near the base (near the groove inside shoulder). Continue placing the sealant on the spigot end of the mating piece on the angled (sloped) joint surface along the top half of the structure, and 6” below the center line on each side, for a total of 12” of sealant overlap. On the spigot end, the sealant should be placed on the slope, near the tip (near the tongue end face).
METHOD A: CONTINUOUS
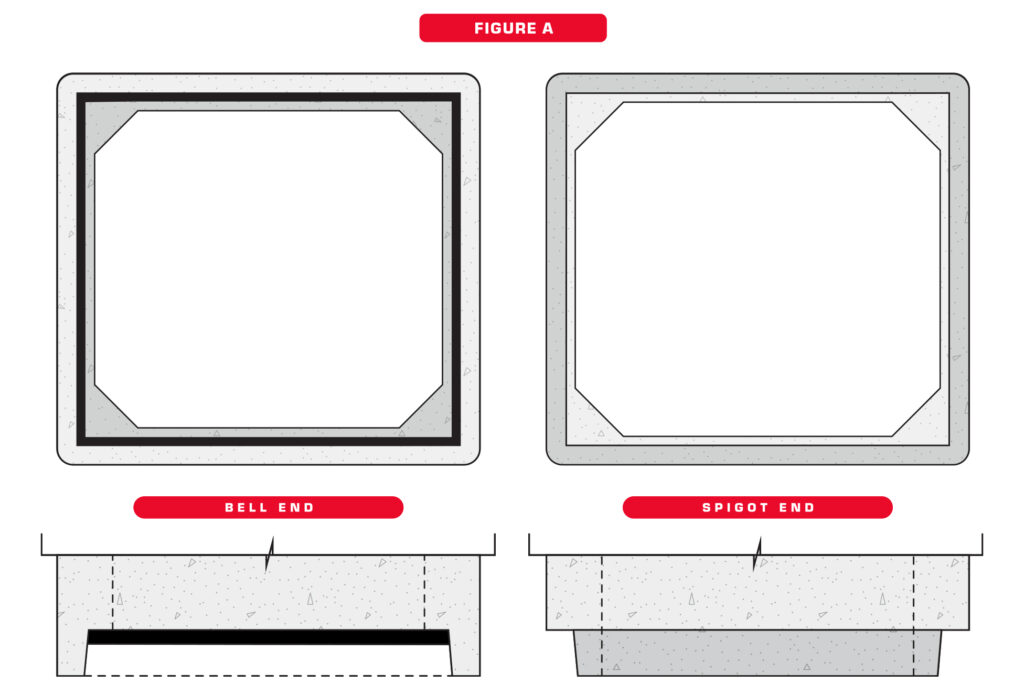
METHOD B: NON-CONTINUOUS
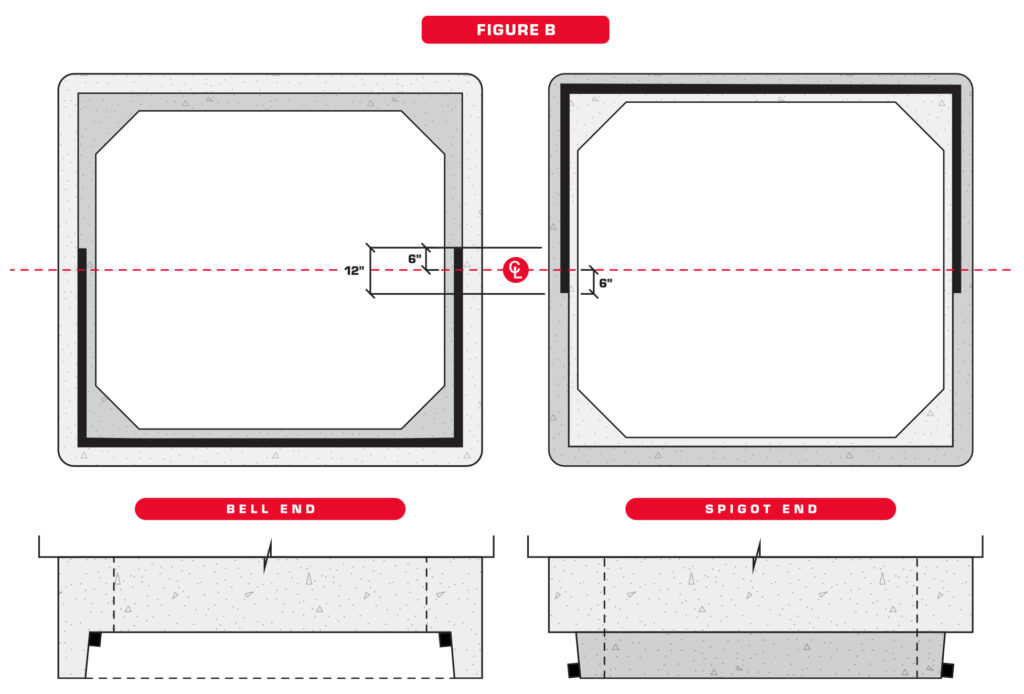
THE PROPER SEALING APPROACH
Different sealing solutions and ConSeal product combinations are needed for different box culvert applications.
The “Level 1: Soil-Tight” approach is the simplest sealing solution. Sealing solutions increase in robustness as the levels increase up to “Level 4: Watertight – Special.”
LEVEL 1: SOIL-TIGHT
APPLICATIONS: Low-risk situations.
EXAMPLES: Stormwater conveyance.
ADVISORIES: Not for use with wastewater, airports, oil, chemicals, holding structures, contaminated soil, contaminated groundwater, or where watertightness is required.
PRODUCTS:
CS-102. Installed using Method A or Method B. OPTIONAL ACCOMPANIMENT: CS-1550 to bond CS-102 to structure.
LEVEL 2: SILT-TIGHT
APPLICATIONS: Low-risk situations.
EXAMPLES: Stormwater conveyance.
ADVISORIES: Not for use with wastewater, airports, oil, chemicals, holding structures, contaminated soil, contaminated groundwater, or where watertightness is required.
PRODUCTS:
CS-102. Installed using Method A or Method B. OPTIONAL ACCOMPANIMENT: CS-1550 to bond CS-102 to structure.
CS-212. OPTIONAL ACCOMPANIMENT: CS-75 or CS-300 to help adhere CS-212 to structure.
LEVEL 3: LEAK-RESISTANT
APPLICATIONS: Low- to medium-risk situations.
EXAMPLES: Stormwater conveyance.
ADVISORIES: Not for use with wastewater, airports, oil, chemicals, holding structures, contaminated soil, contaminated groundwater, or where watertightness is required.
PRODUCTS:
CS-102. Installed using Method A or Method B. OPTIONAL ACCOMPANIMENT: CS-1550 to bond CS-102 to structure.
CS-212. OPTIONAL ACCOMPANIMENT: CS-75 or CS-300 to help adhere CS-212 to structure.
OPTIONAL CS-1500. Installed on the interior joints. If this option is chosen, the joint surfaces to which the CS-1500 is applied must be primed with either CS-80 or CS-85.
LEVEL 4: WATERTIGHT-STANDARD
APPLICATIONS: Medium-to high-risk situations.
EXAMPLES: Stormwater, wastewater, holding structures, or conveyance structures, low- to medium-pressure.
ADVISORIES: Not for use with airports, oil, chemicals, contaminated soil, contaminated groundwater, or high pressure.
PRODUCTS:
CS-102. Installed using Method A or Method B. OPTIONAL ACCOMPANIMENT: CS-1550 to bond CS-102 to structure.
CS-235. Installed using Method A only. OPTIONAL ACCOMPANIMENT: CS-1550 to bond CS-235 to structure.
CS-212. OPTIONAL ACCOMPANIMENT: CS-75 or CS-300 to help adhere CS-212 to structure.
OPTIONAL CS-1500. Installed on the interior joints. If this option is chosen, the joint surfaces to which the CS-1500 is applied must be primed with either CS-80 or CS-85.
LEVEL 5: WATERTIGHT-SPECIAL
APPLICATIONS: High-risk situations.
EXAMPLES: Wastewater, airports, oil, chemicals, contaminated soil, contaminated groundwater, holding structures, conveyance structures, high pressure.
PRODUCTS:
CS-5000. Installed using Method A only. REQUIRED: CS-1550 to bond CS-5000 to structure. REQUIRED: Fast-acting bonding agent to bond ends of CS-5000 together.
CS-212. OPTIONAL ACCOMPANIMENT: CS-75 or CS-300 to help adhere CS-212 to structure.
CS-1500. Installed on the interior joints for greater leak-resistance. REQUIRED: The joint surfaces to which the CS-1500 is applied must be primed with either CS-80 or CS-85.
For other special circumstances, alternative sealant material or combinations of materials may be recommended by the Concrete Sealants engineering team.
INSTALLATION DOS AND DONTS
WHAT INSTALLATION PRACTICES SHOULD BE USED, AND WHAT SHOULD BE AVOIDED?
- The success of any product relies on proper installation.
- Always follow the manufacturer’s recommendations and employ installation best practices:
INSTALLATION DOS:
- Ensure the concrete surface is clean; dry; sound; and free of debris, dust, laitance, form release agent, and any other substances that may inhibit sealant adhesion.
- Prime the concrete surface for best results.
- Use a bedding adhesive for the sealant, as needed, to hold it securely in place during installation of the structure.
- Start and stop the sealant at least 12” away from any corners of the structure.
- Join sealant ends in a butt joint or splice them together at 45-degree angles before kneading them together.
- Knead the ends of sealant together into one continuous, homogeneous rope of sealant.
- Ensure at least 50% sealant compression.
- Be sure to remove the contact paper after sealant installation and before assembling the structures.
- Consult with the Concrete Sealants engineering team for specific guidance.
INSTALLATION DO NOT:
- Stretch the sealant.
- Overlap or stack the sealant ends on top of one another when starting or stopping a rope of sealant.
- Leave gaps or spaces between the adjoining sealant pieces.
- Assume the sealant will be made into a homogeneous rope of sealant by compression alone.
- Assume more sealant is better.
- Assume sealant squeeze-out from the joint corresponds to an improper seal.
GLOSSARY OF TERMS
ANNULAR SPACE: Space between the inner joint mating surface of the female end and the outer joint mating surface of the male end of an assembled pipe, manhole, or box structure joint.
BUTYL RUBBER: Hydrocarbon-based material used in combination with other raw materials to produce many types of preformed flexible joint sealant.
EXTERNAL JOINT WRAP (External Sealing Band, External Joint Membrane): Permanent, flexible membrane applied over the exterior joint surfaces of buried structures to prevent water and soil intrusion.
FEMALE END (Bell, Socket, Groove, Modified Groove): The portion of the end of the pipe, manhole, box structure, or other structure – regardless of its shape or dimensions – which overlaps a portion of the end of the adjoining pipe, manhole or box structure.
GROOVE END FACE: See Figure #0.
GROOVE OUTSIDE SHOULDER: See Figure #0.
GUN-GRADE SEALANT: Caulkable sealing material used to fill remaining joint gap of assembled structures.
HYDROPHILIC: (In reference to waterstop sealants) able to absorb water.
HYDROSTATIC PRESSURE: Pressure exerted by water at rest.
JOINT: A connection of two pipe, manhole, or box section ends.
JOINT GAP, ASSEMBLED: Separation between two adjoining box sections, after assembly, as a result of the joint design, joint sealing material, and installation.
JOINT GAP, DRY FIT: Separation between two adjoining box sections when fit together without sealing material; used in conjunction with other information to determine appropriate sealing material selection, sizing, and placement.
JOINT MATING SURFACE: angled portion of joint in a tongue and groove joint which connects the tongue end face to the tongue outside shoulder, and which connects the groove end face to the groove outside shoulder; often the surface to which joint sealing materials are applied.
LEAK-RESISTANT: Resists leakage to standard test criteria.
MALE END (spigot, tongue, modified tongue): The portion of the end of the pipe, manhole, box structure, or other structure – regardless of its shape or dimensions – which is overlapped by a portion of the end of the adjoining pipe, manhole, or box structure. Preformed flexible joint sealant: rope-style sealing material designed to be compressed in structure joints to prevent water and soil intrusion.
SILT-TIGHT: Installation system intended to prevent silt intrusion in joints; not leak-resistant.
SOIL-TIGHT: Installation system intended to prevent soil intrusion in joints; not leak-resistant.
Disclaimer: This publication is to assist users to understand the proper use of ConSeal’s products. Contact ConSeal’s technical staff for practices and procedures that meet your specific requirement. Concrete Sealants, Inc. does not warranty any improper use of its products.
How can conseal help you today?
- I’m looking for technical resources.
-
I need technical assistance with a ConSeal product.
Connect me with an engineer - I want t talk with a ConSeal engineer about a new project.
- Show me how the products work?